MIM
What Is MIM?
Process Overview
When to Use MIM
General Guidelines
Technology Comparisons
Materials Range
Materials List
Design Guidelines
Designing for Manufacturability
Uniform Wall Thickness
Thickness Transition
Coring Holes
Draft
Ribs and Webs
Fillets and Radii
Threads
Holes and Slots
Undercuts
Gating
Parting Lines
Decorative Features
Sintering Support
Secondary Operations
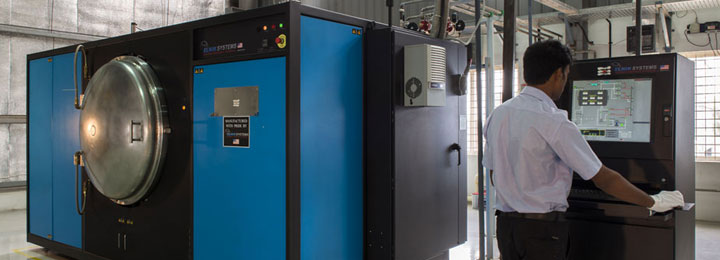
Holes and Slots
Besides being used to reduce part mass and provide uniform wall thicknesses, holes and slots can provide useful functional features in MIM components, and can generally be produced without adding to the piece price. However, adding these features does increase the complexity of the mold, as shown in Figure 8a, which necessarily adds to its cost. Holes that are perpendicular to the parting line are the easiest (and least costly) to mold in. Holes that are located parallel to the parting line, while readily achievable, require mechanical slides or hydraulic cylinders, which increases the up-front tooling costs.
Internally connected holes are possible, as shown in Figure 8b. To prevent potential sealing-off problems and issues with flashing, careful consideration must be given to the design. If possible, one hole should be D-shaped in order to provide a flat on the core pin for a robust tool seal-off, as well as to eliminate inordinate wear of the feathered edges that would otherwise be required on the contoured face of the mating member.
